Current Research Projects
Burns Group Projects
The Burns Research Group is always working on a wide variety of environmental cracking problems. Current research topics, along with student and sponsorship information, can be found in the descriptions below. This list does not include all of the opportunities for undergraduate research nor future PhD and Masters research projects in the Burns group.
Current Research Projects
Effect of Galvanically Induced Corrosion Damage on the Fatigue Crack Formation Behavior of Al 7050-T7451
Researcher(s): Carly Cocke
Sponsor(s): Office of Naval Research (ONR)
Project Description: Galvanic corrosion damage in aircrafts is produced when steel fasteners are coupled with aluminum substructure in atmospheric conditions as shown in the below figure. Interaction of the galvanic corrosion damage with aircraft operational loading poses a challenge on the structural integrity and fatigue behavior of the airframe components. The objectives of this project are to quantify the humid air crack formation life and microstructure scale crack progression from the galvanic corrosion morphologies, and to identify features that govern crack formation process. Corrosion damage is induced under electrochemical conditions representative of a galvanic crevice in atmospheric conditions with and without corrosion inhibitors. 3D characterization of the corrosion damage is achieved using white light profilometry, microscopy and x-ray tomography. Crack formation life (Ni) to ≈10 μm and local microstructure-scale crack growth rates (da/dN) are determined in Al 7050-T7451 exposed in humid air using fractography of load-induced crack surface marker-bands. Data obtained from the characterization of underlying microstructure, 3D corrosion morphology feature, crack formation and crack growth rate will be used to evaluate safe life and damage tolerant engineering models, and to identify the influence of corrosion inhibitors on fatigue initiation behavior.
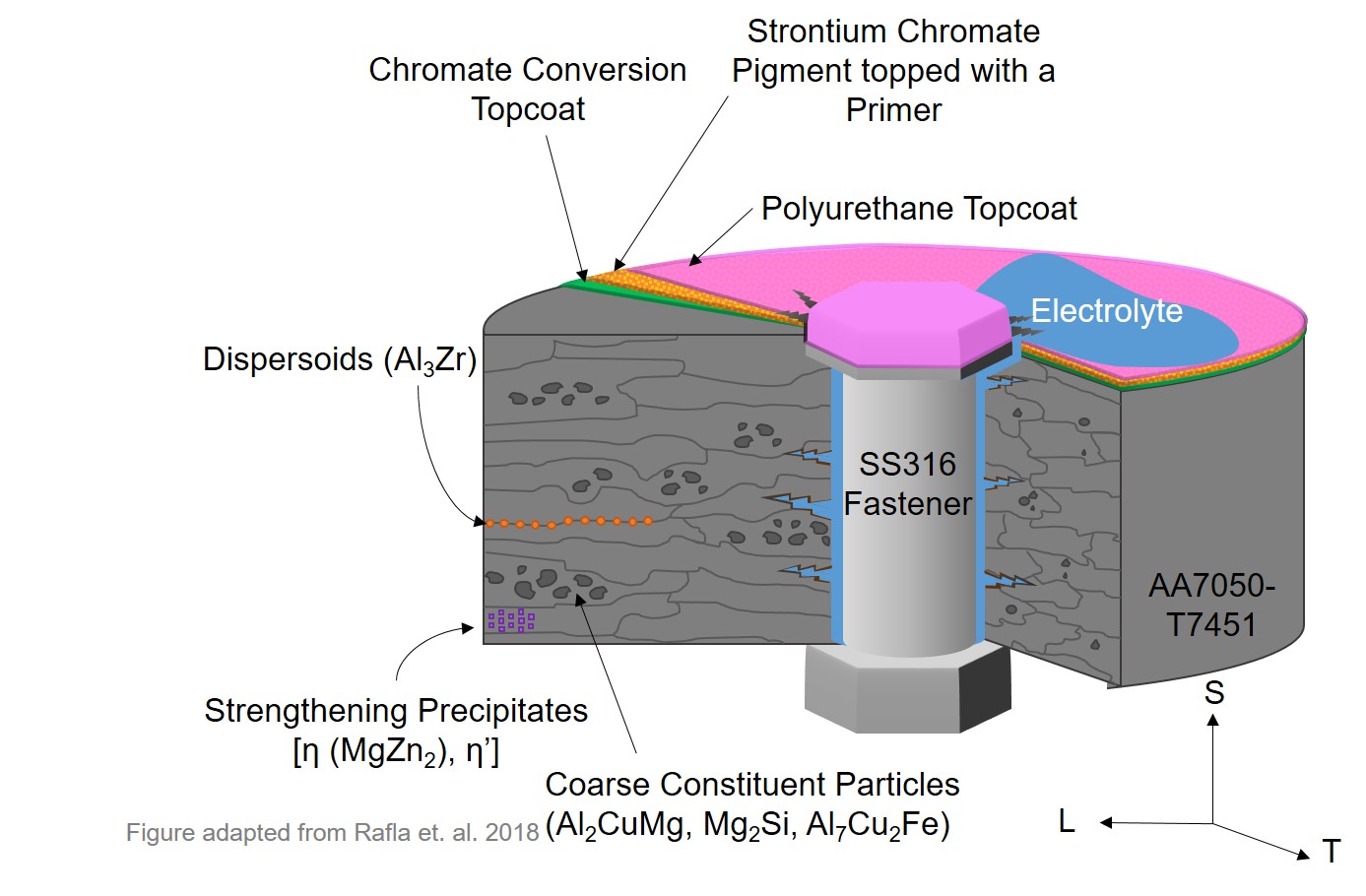
Influence of γ’ Precipitate Morphology on Crack Tip-Damage Interactions in Monel K-500
Researcher(s): Zach Harris
Sponsor(s): DoD Corrosion Office – Technical Corrosion Collaboration
Project Description: Nickel-based superalloys exhibit exceptional mechanical properties and excellent resistance to chemical degradation. However, despite the alloy system’s inherent resistance to chemical attack, they have proven to be susceptible to hydrogen environment-assisted cracking (HEAC) when stressed in aggressive environments that electrochemically produce hydrogen. Though the influence of hydrogen embrittlement on mechanical properties has been well studied, the contribution of microstructural variables with regards to the proposed mechanisms are still unclear. One feature that has yet to be thoroughly evaluated in the literature is the influence of γ’ precipitate morphology on local deformation structures near a crack tip. Furthermore, the effect of changing the precipitate morphology on the accuracy of current micromechanical models used for predicting HEAC kinetics is not known. Thus, a systematic study of the influence of precipitate morphology on HEAC of Ni-based superalloys is needed to not only address identified knowledge gaps in the scientific literature, but to also evaluate the effect of microstructural variability on HEAC modeling. This study will seek to address this need through a three phase approach. First, a metallurgical study will be completed to evaluate the γ’ precipitate morphology as a function of applied heat treatment. These results will also be used to better understand the general slip behavior and slip-grain boundary interactions as a function of the precipitate morphology. Second, the influence of the precipitate morphology on HEAC will be evaluated using fracture mechanics testing on single-edge notched specimens at varying hydrogen concentrations. And third, the influence of the precipitate morphology on the crack-wake damage structures will be evaluated using state-of-the-art characterization techniques.
Mechanistic Studies of Stress Corrosion Cracking Under Atmospheric Exposure Conditions for Nuclear Waste Canister Lifetime Predictions
Researcher(s): Sarah Blust
Sponsor(s): Department of Energy's Nuclear Energy University Program (DOE NEUP)
Project Description: One of the frontiers of corrosion science is stress corrosion cracking (SCC) under atmospheric conditions. This project takes previous stress corrosion cracking experiments performed on Stainless Steel 304L and 316L series alloys under full immersion conditions, and seeks to expand it to various atmospheric environments such as misting, differing salt concentrations, temperatures and other parameters. In particular it will determine to what degree the mechanisms of stress corrosion cracking previously developed for full immersion conditions can be extended to atmospheric conditions. Crack growth kinetics will be measured using direct current potential drop, which allows for micron scale crack extension measurements. The generated SCC crack growth rates will be used to generate lifetime predictions of components using a linear-elastic fracture mechanics-based model. This project will be directly applied to stainless steel used for spent nuclear waste canisters currently in service.
Study of the Relative Localized Corrosion and Cracking Susceptibility of Additively Manufactured and Wrought Corrosion Resistant Alloys
Researcher(s): Michael Roach
Sponsor(s): Office of Naval Research
Project Description: Additively manufactured (AM) alloys offer many potential benefits for the construction of engineering components of importance to the Navy, from reducing waste and time-to-availability to the opportunity for radically new mechanical designs which cannot be constructed from conventionally processed stock products (e.g., plate, rod, sheet). They also may allow the introduction of graded composition within components. Corrosion resistant alloys (e.g., stainless steels, nickel alloys, titanium alloys) are often the base material from which AMA parts are constructed. More recently, precipitation hardened, martensitic stainless steels (e.g., 17-4PH) have become of increasing interest due to their higher strength than austenitic stainless steels. Structural marine applications that require higher strength levels often use precipitation hardened martensitic stainless steels. For such steels manufactured via conventional methods, environmental cracking is often a prominent failure mode in chloride-rich environments; H-embrittlement has been implicated as governing mechanisms for such cracking. As such, it is critical to evaluate the environmental cracking behavior of AM materials to provide rigorous vetting of these materials that will ensure a safe extension to structural applications.
Elucidating the Mechanisms of High Temperature Fatigue Behavior in a Ni-based Superalloy
Researcher(s): Alex Jennion, Zach Harris
Sponsors(s): Rolls-Royce
Project Description: The objective of this research is to understand the relative contribution of oxidation, creep and cyclic damage accumulation to high temperature fatigue crack growth in nickel-based superalloys. In air, fatigue crack growth rates increase with increasing temperature. Under dwell fatigue loading, which are more representative of actual loading conditions, growth rates are higher, increase with increasing temperature, and then decrease at temperatures above 650 ˚C. Current component lifetime models do not account for this change in growth rate and are too conservative. Fatigue testing in air and vacuum at different temperatures, stress intensity ranges, and dwell times will isolate the contribution of specific damage mechanisms. By applying a multi-length scale characterization method to the fracture surface and crack tip, the contribution of oxidation, creep and fatigue can be quantified. This investigation with better inform fatigue-life modeling and design of new high-temperature fatigue resistant alloys.