Research
Development and Validation of Soot Kinetic Models
Combustors of mid-to-large size gas-turbine engines operate under high-pressure conditions, ranging from 25-60 atm. While modern gas-turbine engines have significantly reduced the formation of pollutants, yet very fine soot particles (10-100 nm) can be formed in these engines. The objective of this project is to collect high-quality soot particle formation and oxidation data under more realistic high-pressure conditions to validate soot kinetic models. The validation experiments are being performed using several laboratory-scale reacting flow configurations (tube reactors and counterflow flames). Once validated, the models developed will be used in simulations of complex multi-dimensional reacting flow simulations of interest to the sponsor of this work, i.e. Rolls-Royce.
Regenerative/Endothermic Fuel Cooling and Modeling
In modern gas turbine engines and in hypersonic engines, some surfaces can easily exceed material temperature limitations if not actively cooled. One concept is to use the fuel itself to regeneratively cool such hot surfaces by taking advantage of the endothermic pyrolysis process. The pyrolyzed fuel typically has better flame holding and overall combustion properties. One negative aspect of this concept is fuel coking in the cooling lines due to PAH/soot formation. As part of an AFOSR-funded Basic Research Initiative, new class of catalyst is being explored to mitigate the coking issue by promoting carbon-carbon bond breaking rather than dehydrogenation reactions. Specifically, optimal pairing of fuel and catalysts are explored with maximum endothermicity and minimum coking tendencies.
Modeling Laser Ablation of Porous Carbon Surfaces
The focus of this project is to understand the laser-material-flow interactions relevant for missile defense systems and reentry vehicles. A detailed numerical model is being developed that takes into account the interaction between heterogeneous combustion of porous and nonporous carbon surfaces with the external homogeneous combustion. The heterogeneous model developed includes the transport and combustion within a porous particle; hence the model can effectively decouple the physical fluid dynamical effects from the intrinsic surface reaction rates. The supporting experiments to validate the model are being performed by the Air Force Institute of Technology using TELOPS hyper-spectral camera capable of measuring the reacting flow structure. This work is supported by the Air Force Office of Scientific Research.
Development of Reduced Kinetic Models
Elementary reaction pathways that describe the pyrolysis and oxidation hydrocarbon fuels typically consist of 100s of species in over 1000 reaction steps. The objective of this work is to derive systematically developed reduced reaction models for engineering applications based on characteristic physical and chemical time scales. Specifically, efficient implementation of reduced reaction models in time-dependent, multi-dimensional hypersonic reacting flow simulations is the key focus of this work. Reduced reaction models developed to date include methane-air, ethylene-air, heptane-air, n-dodecane-air, and JP-10-air.
Modeling Chemical Vapor Infiltration Process of SiC Synthesis
Once validated, the models developed will be used in simulations of complex multi-dimensional reacting flow simulations of interest to the sponsor of this work, i.e. Rolls-Royce.
Development of Advanced Non-intrusive Laser-Based Diagnostics
Recent Research Developments
-
Fuel Experiments
Fundamental experiments and modeling to understand and control fuel pyrolysis, oxidation, and coking.
-
Flame Stabilization Mechanisms
Understanding of flame stabilization mechanisms of high-speed reacting flows
-
Reduced Reaction Models
Development of reduced reaction models for soot formation and oxidation for CFD applications.
Grants
-
Turbulent Flame Structure of Cavity Stabilized Reacting Shear Layers
NSF-Air Force
-
Stationary Mixed Metal-Oxide Acid Catalysts for Endothermic Fuel Decomposition and Enhanced Ignition/Flame Holding Characteristics
Air Force Basic Research Initiative
-
Mechanism of Soot Particle Formation Under High Pressure Conditions
Rolls Royce
-
Chemical Vapor Infiltration in SiC Synthesis
Rolls Royce
-
Merging Hyperspectral Imagery and Multi-Scale Modeling for Laser Lethality
Air Force
Contact Information
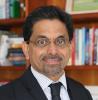
Harsha K. Chelliah
Professor Chelliah is currently serving as the Program Director for Combustion and Fire Systems in the Division of Chemical, Bioengineering, Environmental and Transport Systems at the National Science Foundation (NSF). His research interests are vast and include fundamental investigations on interaction of finite-rate kinetics with transport.