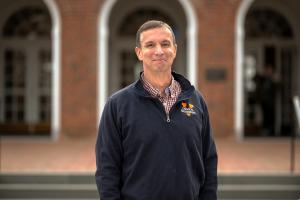
A team of engineers is reimagining one of the essential processes in modern manufacturing. Their goal? To transform how a chemical called acrylonitrile (ACN) is made — not by building world-scale manufacturing sites, but by using smaller-scale, modular reactors that can work if they let the catalyst, in a sense, “breathe.”
ACN is everywhere, from carbon fibers in sports equipment to acrylics in car parts and textiles. Traditionally, producing it requires a continuous, energy-intensive process. But now, researchers at the University of Virginia and the University of Houston have shown that by pausing to “inhale” fresh oxygen, a chemical catalyst can produce ACN more efficiently. This discovery could open the door to smaller, versatile production facilities that adapt to fluctuating needs.
William Epling, a professor and chair of the Department of Chemical Engineering at UVA, calls the technique “forced dynamic operation,” or FDO. Picture a machine cycling through work and rest periods, using short breaks to recharge and perform at its best. This is what Epling’s team has done with an industrial bismuth molybdate-based catalyst, alternating between two phases: one containing the full mixture of ingredients needed to make ACN, and another containing only oxygen. This rhythmic approach allows the catalyst to regenerate its lattice oxygen — the source of the key reactant in driving the transformation into ACN.
“FDO is essentially like giving the catalyst a breather, letting it work harder and more effectively in each cycle,” said Zhuoran Gan, a Ph.D. candidate in Epling’s lab. When the catalyst "rests" with just oxygen, it regains strength to tackle the next cycle of production. The results were surprising: ACN production was exceeded by as much as 30% over traditional, continuous methods.
The impact could be transformative. Smaller production facilities that use this method could meet the demand for ACN growth without the need for world-scale, capital intensive plants. Such facilities could also operate closer to end-users, like manufacturers of high-performance carbon fibers, reducing transportation costs and making production more adaptable. Epling envisions a future where chemical manufacturing can be more flexible and efficient, with small, scalable production units that meet demand exactly where and when it arises.
With support from the Department of Energy and industrial partners, the UVA team’s work underscores how sometimes, a catalyst just needs a breath of fresh air to become a powerful tool for innovation.
The article, titled "Propene Ammoxidation over an Industrial Bismuth Molybdate-Based Catalyst Using Forced Dynamic Operation," was authored by Zhuoran Gan and William S. Epling from the Department of Chemical Engineering at the University of Virginia, alongside James F. Brazdil and Lars C. Grabow from the William A. Brookshire Department of Chemical and Biomolecular Engineering at the University of Houston.