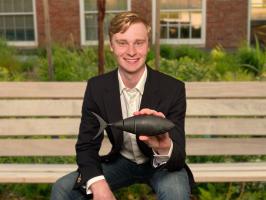
He’s known as “The Tunabot Guy” — the University of Virginia postdoctoral researcher who is testing the limits of a bioinspired robotic fish modeled after high-performance tuna. And with his ongoing dedication to the effort, those limits just keep getting pushed.
Double ’Hoo Carl White — a Bachelor of Science and Ph.D. recipient from the School of Engineering and Applied Science’s Department of Mechanical and Aerospace Engineering — works in Professor Hilary Bart-Smith’s Bio-Inspired Engineering Research Laboratory, dedicating his efforts to the development and testing of Tunabots as a postdoctoral fellow. Drawing inspiration from the exceptional speed and endurance of tuna, White's mission centers on bridging the gap between biology and engineering to develop autonomous underwater vehicles (AUVs). Whereas AUVs are traditionally propeller-driven tubes, bioinspired vehicles based on fish have bodies with complex, undulatory motions.
“The Tunabots are testing platforms that further our understanding of high-performance fish and how we can harness their remarkable capabilities to inform AUV design,” said White, who was a part of Bart-Smith’s team that worked alongside Harvard researchers to test the previous Tunabot in 2019.
In 2021, White unveiled the new generation named Tunabot Flex, which demonstrated that when the body flexibility of tuna is applied to the robot, its swimming performance is vastly improved. It was also faster and more than twice as efficient as its equally sized predecessor. This unprecedented combination of swimming speed and efficiency significantly advanced the field of bioinspired underwater vehicles. It also led to the acquisition of competitive funding from the Office of Naval Research and collaborations with other top scientists and Boston Engineering, a research and development firm, to further develop the technology.
“Tunabot Flex’s remarkable agility, efficient propulsion and ability to navigate complex underwater environments hold great promise for advancements in underwater exploration, environmental monitoring and underwater robotics,” Bart-Smith said. “It serves as a testament to the boundless potential of bioinspired engineering and paves the way for exciting possibilities in underwater robotics research and applications."
White designed Tunabot Flex using reference material of tuna provided by biologists at Harvard University’s Lauder Laboratory — such as high-speed video, photographs and a 3D model of tuna — and traveled there for experiments. Despite the lab having a custom-flow tank capable of high-speed conditions, Tunabot Flex cruised at the tank’s upper limit with a voltage input of just 60%. This meant that Tunabot Flex could have flapped much faster, generating even higher speeds, but was untestable due to the flow tank’s limits. Nevertheless, the tested speeds and corresponding energy efficiencies of Tunabot Flex were already exceptional.
“The fact that Tunabot Flex maxed out our tank signifies a leap forward in our understanding of aquatic locomotion,” said Harvard Professor George Lauder.
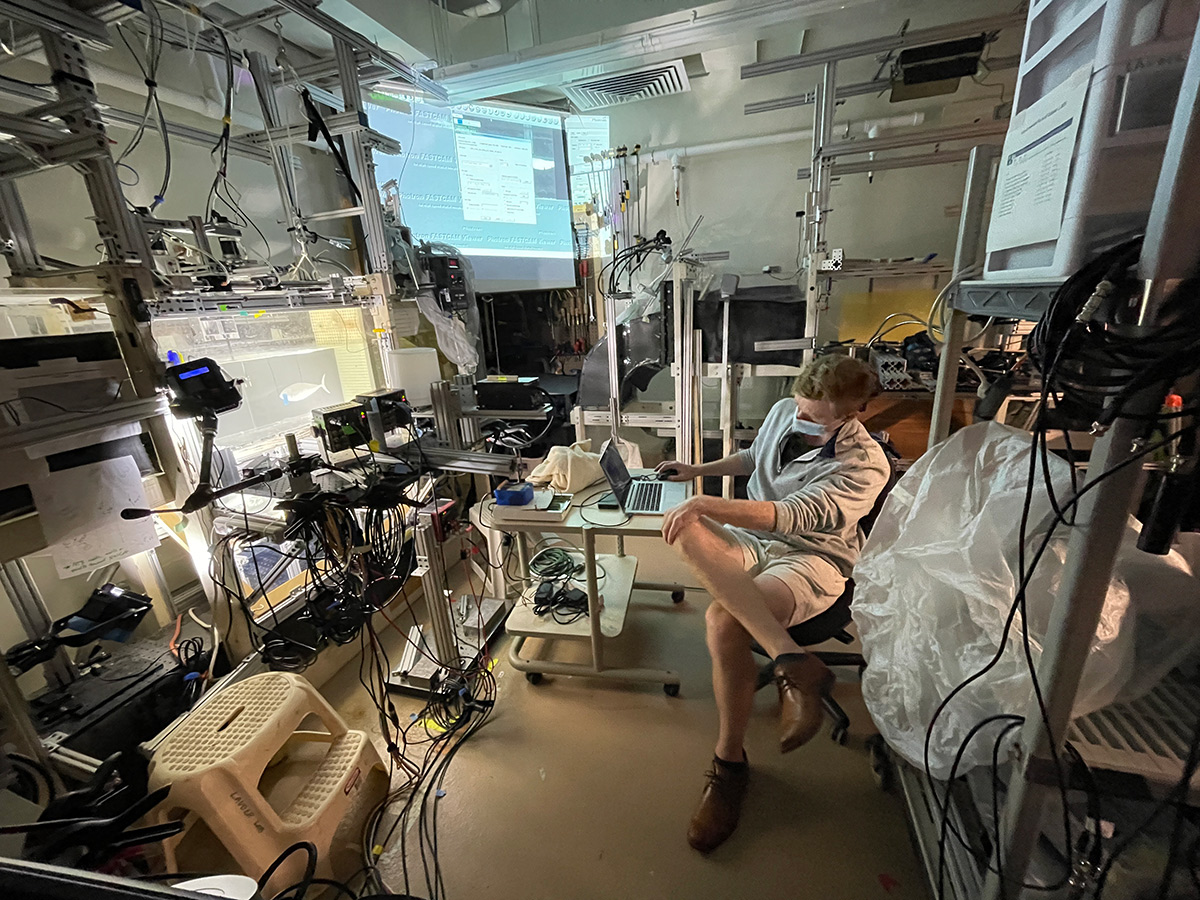
White, too, saw the significance of those Harvard tests.
“There is a crucial tradeoff between speed and energy efficiency for bioinspired AUVs,” White said. “Robotic fish are currently unable to match the combined swimming speed and efficiency of high-performance fish. If this gap were to close, the potential for AUVs would be significant. One day, AUVs may even outperform fish.”
While continuing his fruitful partnership with Lauder and the Lauder Laboratory, White also collaborated with postdoctoral fellow Robin Thandiackal to investigate the intricacies of linear acceleration from rest using Tunabot Flex.
“Understanding the mechanisms and dynamics involved in accelerating from a stationary position is crucial in various fields, including robotics, biomechanics and vehicle engineering,” Thandiackal said. “The research sheds light on the intricate interactions between body and fluid and how thrust forces are generated during the process of linear acceleration, offering a deeper understanding of how organisms and engineered systems achieve efficient and rapid movement.”
This year, White has lent his expertise to Princeton University Professor Radhika Nagpal's new lab, assisting it in adapting the proven design of Tunabot Flex for its own robotic fish, which will swim in groups like schools of fish.
“I see ecology as a model for robotics,” Nagpal said. “I envision robot teams that seamlessly blend into their environment, minimizing waste and disruption to ecosystems, just like nature.”
White added: “Schooling behavior offers a collective efficiency boost. A group of robotic fish could coordinate to quickly complete a task, such as surveying or repairs, and then swim in a school to the next location — all while minimizing ecological disruption.”
Currently, White is fully immersed in the highly competitive Small Business Technology Transfer program that partners small domestic businesses with nonprofit research institutions like UVA to conduct federal research and development. Through this program, White is supporting Boston Engineering’s development of a robotic fish for the Office of Naval Research. Since successfully defending his dissertation last fall, White has dedicated himself to Phase I of the program. Boston Engineering and UVA were recently selected for a highly competitive Office of Naval Research Phase II award that will support continued advancement.
“Representing UVA is an exciting responsibility, and it’s motivating to know that my work directly contributes to our success,” White said.
White reports directly to Boston Engineering and conducts vital experiments on its behalf at UVA. For these experiments, White employs a bigger version of Tunabot Flex known as Tunabot Flex X2, or TFX2. Measuring 51 centimeters in length, TFX2 doubles the dimensions of the 25.5-centimeter Tunabot Flex. Boston Engineering’s interest in scalability fueled this size increase as the company references Tunabot Flex for the design of its own vehicle which will be even larger than TFX2.
“A key advantage of Tunabot Flex X2 is how it can be energy efficient in demanding underwater conditions, such as in strong currents and tight spaces,” said Michael Rufo, the vice president of research and development for Boston Engineering. “Its design and flexibility can enable bioinspired thrust with precise control and agility.”
Using TFX2’s modular design, White also investigates the benefits of various design features, both bioinspired and “beyond-bio” — features that are not found in nature. Engineers can design and manufacture body parts that would otherwise be impossible due to evolutionary pressures or the properties of biological material, producing artificial evolution in the blink of an eye. Boston Engineering’s state-of-the-art AUV leverages these invaluable insights gained from Tunabot Flex and TFX2 to push the boundaries of scale and performance.
“This foray into industry research pivoted away from my typical academic projects, providing me with a remarkable learning experience,” White said. “I’m sincerely grateful for the many incredible opportunities such as this that have defined my time at UVA.”
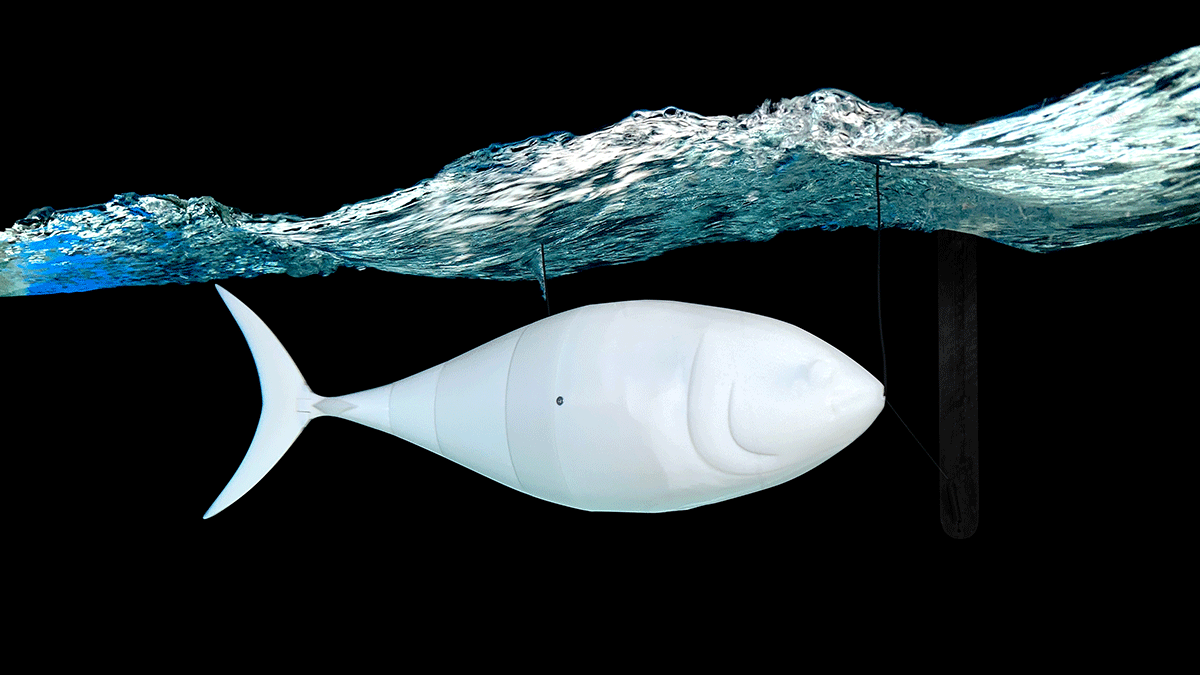