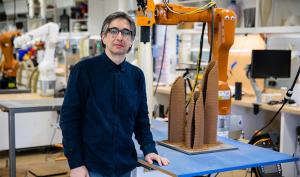
Someday, maybe sooner than later, people building homes and offices may be able to 3D-print their roofs and walls using soil implanted with seeds – think oversized Chia pets – thanks to new sustainability research at the University of Virginia.
You’ve probably seen buildings with roof-top gardens and terraces that support trees and grasses. It’s cumbersome for architects and builders to graft soil and plants onto steel and cement, although the environmental payoffs can be big: gardens are natural insulators, soak up rain and provide green spaces for people, animals and pollinators.
Ji Ma, an assistant professor of materials science and engineering at UVA’s School of Engineering and Applied Science, wondered: “Why do we have to make it so that the structure or building is separate from the nature it sits in?”
To answer this question, Ma forged a partnership with David Carr, a research professor in UVA’s Department of Environmental Sciences, and Ehsan Baharlou, an assistant professor in UVA’s School of Architecture. He also enlisted one of his students, Spencer Barnes, who joined Ma’s research group as a first-year undergraduate and earned his Bachelor of Science in aerospace engineering in May 2022.
Together, they have proven that 3D-printing geometrically complex structures made of soil and seed is doable — introducing a key innovation in bio-based construction.
3D printing, or additive manufacturing, in architectural design and building construction is an emerging market, driven by community interest in green buildings and a need for affordable housing. Project Virginia exemplifies this trend. Alquist 3D, a builder of 3D-printed homes, launched Project Virginia to offer affordable and sustainable homes to people living in remote and underserved regions of the United States. The company broke ground on the project in Pulaski, Virginia, in late April, with plans to complete 200 homes in Pulaski and Roanoke by 2027.
The UVA research team is taking 3D-printing one step further, to combine additive manufacturing’s speed, cost efficiency and low energy demands with locally resourced, bio-based materials. This design philosophy and approach aligns with a sustainable development practice called the circular economy.
As explained by the Ellen MacArthur Foundation, a circular economy delivers better outcomes for people and the environment by eliminating waste and pollution, circulating products and materials at their highest value and regenerating nature. In our current economy, we take materials from the Earth, make products from them, and eventually throw them away as waste – the process is linear. In a circular economy, by contrast, we stop waste being produced in the first place.
“We moved to soil-based ‘inks’ to derive additional benefits from circular additive manufacturing,” Baharlou said. “We are working with local soils and plants mixed with water; the only electricity we need is to move the material and run a pump during printing. If we don’t need a printed piece or if it isn’t the right quality, we can recycle and re-use the material in the next batch of inks.”
Circular bio-based construction relies on more efficient use of raw materials in construction, in turn helping to reduce carbon emissions during the life cycle of a building. Not only are most components and materials used in the construction industry not adaptable, reusable or recycled during or after their lifecycle, they are often not locally sourced. Breaking away from the current linear approach to designing and constructing buildings to a circular one requires research and prototyping across architecture, engineering and construction.
That’s where Barnes entered the picture.
“They paid me to play with dirt,” Barnes said.
“Professor Ma has a very sophisticated additive manufacturing lab, working mostly with laser printing with metal powders. The printers are high-end, very precise and shiny. Then there’s me at the corner table mixing up some soil concoction.”
Barnes conducted experiments with soil-based inks, supported by a University of Virginia Harrison Grant. Using a desk-sized 3D-printer, he explored two approaches, printing soil and seed in sequential layers and mixing seed and soil before printing. Both approaches worked. Barnes produced a cylindrical prototype, about the size of soda can, which looked a bit like a Chia pet.
Baharlou then proposed 3D-printing soil structures with more complex geometries, such as domes. The research team, including Leah Kirssin, who earned a Bachelor of Science in architecture in 2021, and Lizzie Needham, who graduated with a Master of Landscape Architecture in the same year, tested how material comes out of the printer head or nozzle, a process called extrusion, without any additives to the soil mixture. These collective efforts revealed that 3D-printed soil structures can support plant growth but would likely be limited to plants that can survive with little water.
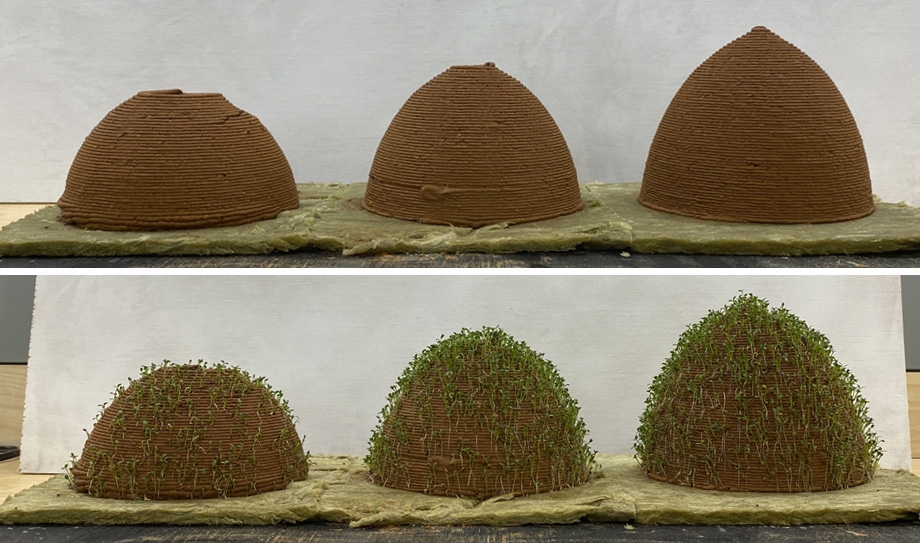
“3D-printed soil tends to lose water more quickly and keeps a stronger grip on the water it has,” Ma said. “Because 3D printing makes the environment around the plant drier, we have to incorporate plants that like drier climates. The reason we think this is the case is because the soil gets compacted. When the soil is squeezed through the nozzle, air bubbles are pushed out. When the soil loses air bubbles, it holds onto water more tightly.”
When a plant wants water, it has to fight the soil for it, exerting some pressure to lure the water from the soil and into the roots. At the same time, the soil exerts pressure of its own to retain water, referred to as matric potential. Whether the plant or the soil wins this tug-of-war depends on the type of soil, the variety of plant and the plant’s maturity. To determine which plants can be grown in 3D-printed soil, Barnes explored the relative availability of water held in a soil over time, in combination with the amount of energy plants needed to extract the water.
To find the right mix of soil and seed, Ma reached out to Carr, who serves as director of Blandy Experimental Farm, an environmental science field station in Clarke County, Virginia.
“Some of my students have used 3D printing to make devices to collect pollen off of bees as they enter their hives, but I never imagined that you could potentially print something that was biologically alive,” Carr said.
Carr provided early advice on a range of soil properties. In addition to holding water, the soil needs to accumulate organic material and store nutrients. It also needs to allow the plants to get a root hold on the printed structure, so that once they get of any size they don’t disappear or get washed off, or desiccate and die.
Carr proposed plants that naturally occur in areas where life is at its limits — native plants that grow practically right on bare rock. “Green roofs tend toward these species that are good at living under these really harsh conditions, getting baked in the sun,” Carr said. “From this research, we can learn a lot about what works for green roofs to help with rain water, cooling and providing a habitat for pollinators and other insects.”
Carr recommended stonecrop as a good candidate for 3D-printing soil structures. Stonecrop, formally known as genus sedum, is commonly used in green roof settings. Stonecrop’s physiology is similar to the cactus. It can survive on very little water, dry out and desiccate to some degree, and then recover.
The team published its results, 3D Printing of Ecologically Active Soil Structures, in the journal Additive Manufacturing earlier this year. Barnes, who first-authored the team’s paper, will continue to help solve big problems with big impacts as a graduate student in mechanical engineering at Stanford University, where he plans to focus on hypersonic flight and propulsion research.
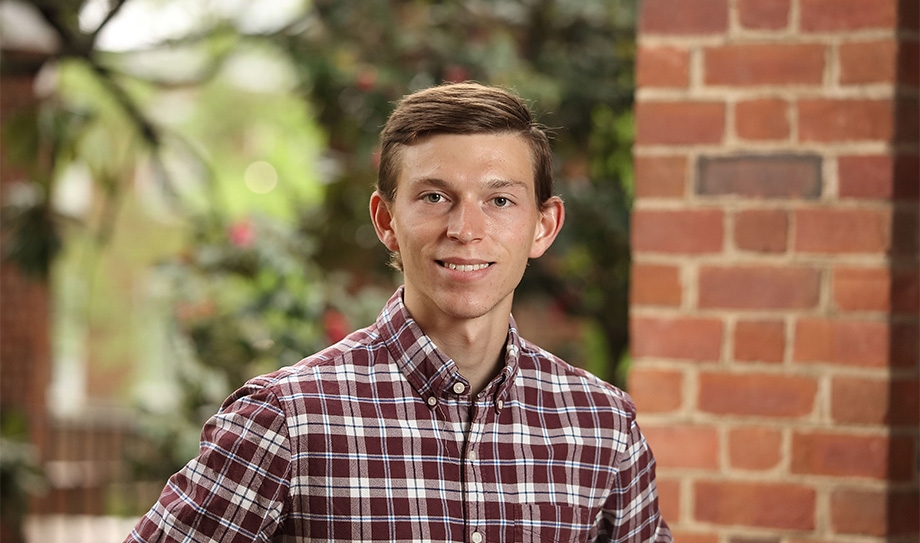
"I greatly enjoyed working with Dr. Ma and the rest of the team,” Barnes said. “The combination of experts from different disciplines culminated in a unique project with big potential impact. I hope to continue working with similar interdisciplinary teams as I head to graduate school."
Ma, Baharlou and Carr have since expanded their research in 3D-printed soil structures, taking advantage of two 3Cavaliers program grants. UVA’s Office of the Vice President for Research established and manages the 3Cavaliers grant program to help faculty from different schools work together.
Ma and Baharlou previously partnered with Osman Ozbulut, an associate professor of civil engineering and principal investigator on a 3Cavliers grant to develop a 3D-printing technique for cement-based architectural structures.
Supported by the School of Architecture’s Fabrication Lab, or FabLab, Baharlou used this 3Cavaliers grant to establish an additive manufacturing fabrication system to 3D-print large structures. The centerpiece of the fabrication system is an industrial robot with a 3- to 4-foot reach that can deposit materials customized to an architect’s desired objectives for a structure, such as space, function and geometry. Baharlou modified this system to create a printer that combined an extruder with an industrial robotic arm to conduct the soil structure experiments.
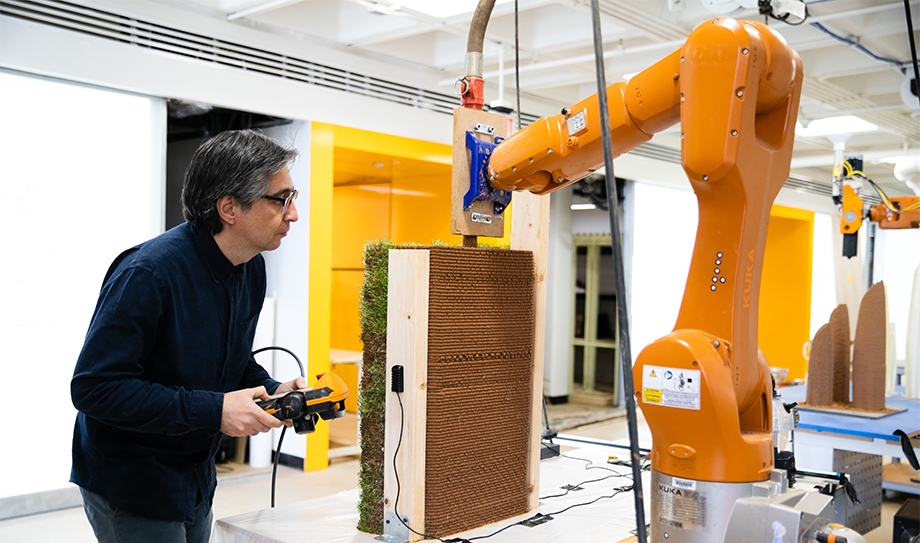
More recently, Ma and Baharlou earned a 3Cavaliers grant with Tomonari Furukawa, UVA professor of mechanical and aerospace engineering, to pursue research in ecological construction. They envision installing Baharlou’s 3D-printing system on a moving robot. A mobile platform could enable 3D-printing multi-sided, complex structures such as a serpentine wall. Baharlou and Ma are also conducting experiments with other biodegradable materials including hemp.
“The team at the Office of the Vice President for Research has been instrumental in spurring collaboration between architects and engineers,” Baharlou said. “Our collaborative projects do more than demonstrate how to use local materials and provide improved quality of construction for buildings manufactured at a very fast pace. Our cross-discipline integration is helpful for society and humanity by advancing the applications of bio-based materials.”
A benefit of the 3Cavaliers grants is the demonstration effect, enabling researchers to collect data and build prototypes to garner awards from major funding agencies such as the National Science Foundation. Ma, Baharlou and Carr are optimistic about pursuing this research agenda. Next steps including formulating soil inks for a larger structure, perhaps one story tall, anticipating that this larger dimension will exacerbate problems such as soil cracking. They are also experimenting with multiple materials layered within a wall panel to insulate the inner wall and maintain moisture for the outer wall.
“Regardless of the material – plastic, metal, clay, soil or plant life – in the end it’s a materials problem,” Ma said. “The additive manufacturing process creates uncertainties and opportunities within the material system you’re working with that’s different from conventional systems. You can approach this in different ways. You can try to avoid it and be afraid of it. Or you can try to control it and take advantage. That’s the long-term goal of our research program.”