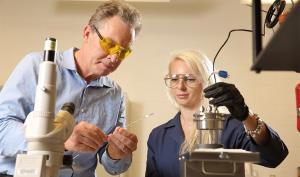
Battleships and aircraft carriers are the superstars of naval sea power. Often overlooked are the smaller and faster vessels, a class called the littoral combat ship that has proven its worth busting drug runners. The USS Wichita put its capabilities on display in 2021 when it intercepted a speed boat carrying $17 million in illegal drugs.
This is just one way that the littoral combat ship provides for homeland defense, protecting coastal waterways from threats that are hard to detect or predict. Despite such successes, the littoral combat ship’s contribution to U.S. sea power appears to be short-lived. The Navy Times reported in May 2022 that half the littoral combat fleet is suffering from structural defects that have led to hull cracks on several vessels, limiting the speed and sea conditions some ships can tolerate.
The culprit is fatigue, which causes materials to fail after repeated cycles of stress.
“Metal fatigue often starts with corrosion,” said John R. Scully, Charles Henderson Chaired Professor of materials science and engineering at the University of Virginia School of Engineering and Applied Science. The metal dissolves, which forms a pit or fissure that creates concentrated stress causing hairline fractures on and below the surface of the material.
“It’s like a wildfire,” Scully said. “The pit is like a tree that catches fire after being hit by lightning. The fire spreads across the whole forest based on how close the trees are, the direction the wind is blowing, the topography of the land, environmental conditions and so on.”
Applying this analogy to the materials used in the littoral combat ships and other fast-moving vessels, it is hard to predict when lightening will strike and how the fire will spread. In other words, how does the wave of corrosion form an array of pits, and how far and fast will the worst pits appear and grow, triggering hairline cracks?
Scully is leading a multi-university research team to answer these questions, involving professors from UVA, Florida State University and Saint Louis University. Together, they will design coatings and new alloys that use material interfaces in an adaptive, responsive way to achieve higher anti-corrosion properties.
A framework of modeling and experimentation helps them understand the fundamental factors that govern pitting, cracking and resulting damage on fatigue life, and how to counter corrosion that begins and evolves on lightweight aluminum and magnesium alloys exposed to saltwater and sea spray. A four-year, $4.3 million grant from the Defense Advanced Research Projects Agency supports their work.
“If we are successful, we can help DARPA achieve a breakthrough to predict when aircraft need to be maintained and when ships, ferries and fast-moving vehicles need to be inspected,” Scully said.
Istvan KissI, professor of chemistry at Saint Louis University, and Oliver Steinbock, professor of chemistry and biochemistry at Florida State University, are working on mathematical or physics-based models of corrosion behavior leading to fatigue.
“The DARPA announcement was very interesting because it pointed to the similarities of structures found in biology, specifically morphologic structures like the shape of an embryo, the stripes of a zebra or spots of a leopard, and the corrosion patterns that sometimes form in metals,” Kiss said. “DARPA asked the scientific community to think about corrosion this way, to find inspiration from this work on morphogenesis.”
“Our models incorporate electrochemical aspects of the corrosion process,” Steinbock said. “Imagine chains of elements that are waiting to react and ultimately relay corrosion damage deep into the material, similar to chains of dominoes knocking over their neighbors.”
Kiss and Steinbock can simulate the corrosion process, taking into account variations in electricity, chemistry, transport and potentially the structure of the alloy itself.
“Our main goal is to improve predictive power,” Steinbock said. “If we get raw data from materials characterization and experimentation, maybe we can simulate some hidden aspects, test some mechanisms, and then predict with high accuracy — up to 90% — what the initial corrosion cell will do in the future.”
Their modeling will provide insight into the corrosion process with possible solutions or mitigation strategies and speed up testing.
“The most important thing is finding the process that accelerates corrosion, what we call activation pathway,” Kiss said.
Corrosion reactions often take place through a myriad of chemical reaction steps with their own complex mathematical descriptions. Kiss and Steinbock look for the simplifying principles of the rates of chemical reactions, a field of research called reaction kinetics. Kiss developed expertise in reaction kinetics at UVA Engineering, working as a post-doctoral fellow and research scientist in chemical engineering. He studied how corrosion waves spread on nickel and iron.
“This early work was very much two-dimensional, corrosion’s growth and spread across a surface,” Kiss said. DARPA’s funding will enable Kiss and Steinbock to model how corrosion not only spreads across a surface but also how it drills down into the material, making the computationally complex leap from 2D to 3D models.
Scully and James T. Burns, Heinz and Doris Wilsdorf Distinguished Research Professor of materials science and engineering at UVA, will inform their models with a deep understanding of corrosion, electrochemistry and fatigue fracture, research strengths of UVA Engineering’s Department of Materials Science and Engineering.
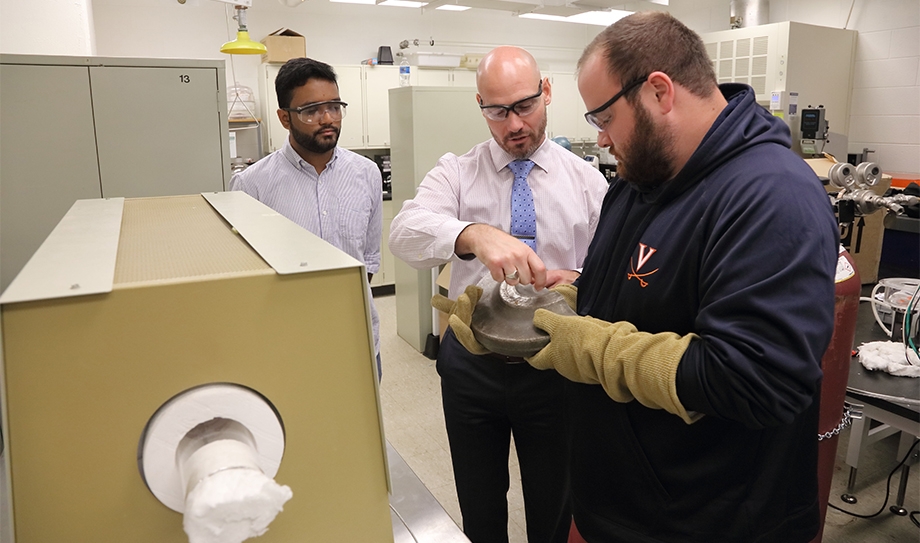
“My aspect of the problem is the interaction of corrosion and mechanics and predicting fatigue behavior,” Burns said. “The idea is to identify the factors present when a crack starts and propagates, and then figure out which one of those features are the bad guys.”
Assuming that corrosion is the first step in damage evolution, Burns’ group couples that corrosion behavior with repeated stressors, called cyclic loads. They have a record of success assessing the effect of cyclic loading on a part’s structural integrity over its lifetime.
“Having an opportunity to reach outside the department and learn from some of the best scientists working in chemical engineering and material simulations, that’s pretty cool,” Burns said. “It will push our group forward by diversifying the material systems and modeling approaches that we use and understanding whether the models are sensitive to material systems or offer global applicability.”
The Scully and Burns research groups, along with faculty and students working in the UVA Center for Electrochemical Science and Engineering, will use a suite of electrochemical and surface characterization techniques to conduct their investigations, including novel fatigue experiments on corrosion-damaged specimens and protective coatings, to identify bad features in the materials.
UVA teammates Ji Ma, assistant professor of materials science and engineering, and James Fitz-Gerald, professor of materials science and engineering, are working on ways to change the composition of a material and its separate layers to impede corrosion and cracking.
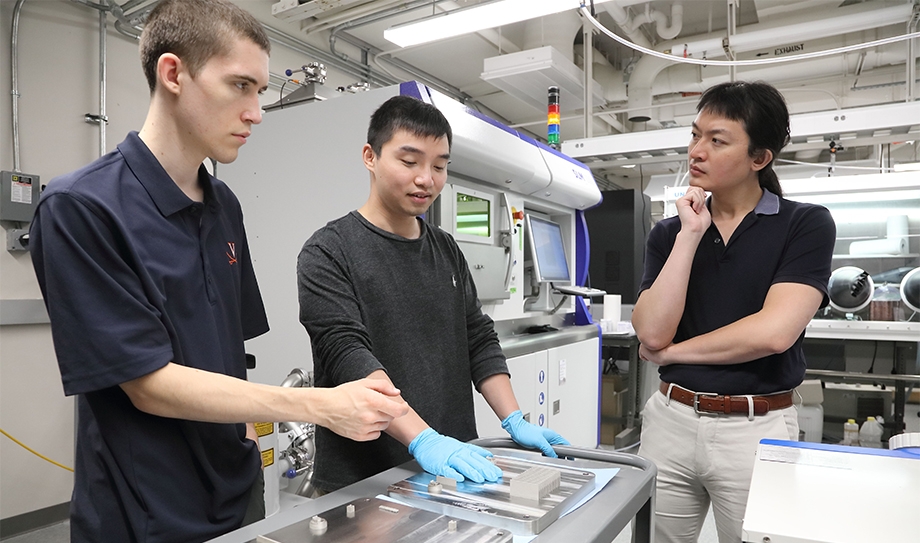
Returning to Scully’s analogy of a corrosive pit to a lightning strike, these material features would be the fire breaks. Ma uses a different analogy, in which the corrosion process is a wave.
“A little part of the material starts to corrode,” Ma said. “Instead of growing in a uniform way, with corrosion everywhere, this little spot will propagate and carry energy forward. So all of a sudden, you have this explosive growth in the part of the material that is corroded.”
Ma and Fitz-Gerald want to control this explosive process by introducing surface and sub-surface features to stop it, which Ma calls wave-breakers. “Think of a sea coast; we build structures like sand bars, reefs and dunes, so that when waves come across, the structures absorb the energy, reducing erosion.”
Ma’s role is to make these tiny islands or little barrier reefs in the material’s structure. Conventional techniques such as surface coating and thin films pose difficulties in controlling precise geometries of the islands and reefs.
Ma’s research in additive manufacturing offers finer control of what these features look like and their material composition. Additive manufacturing is another research strength of UVA Engineering’s Department of Materials Science and Engineering.
“This is a new way of applying additive manufacturing, as a materials modification tool rather than a printing tool,” Ma said. “It’s all theoretical at this point because nobody’s really done it. Our role is figure out how to do that.”
The project depicted is sponsored by the Defense Advanced Research Projects Agency. The content of this story does not necessarily reflect the position or the policy of the Government, and no official endorsement should be inferred.