Hot Corrosion
Molten Salt Deposit Assisted Corrosion of CMCs and Alloys
Na2SO4 and MgSO4, derived from fuel and the external environment in an engine environment, deposit on both ceramic and metal components. The Opila research group is working to understand the effects of these deposits on component lifetime.
Hot Corrosion of CMCs
Inside of marine-based turbine engines, a new set of materials are needed for the higher temperatures required for increased engine output. The operating environment in marine-based turbine engines causes reactions between turbine components, gaseous engine fuel, and ocean water to be severe. At the high operating temperature of marine-based turbine engines, molten Na2SO4 salts form, and cause turbine engine materials to react violently, leading to hot corrosion. New Silicon Carbide (SiC) based Ceramic Matrix Composite (CMC) materials, and their reactions in this engine environment must be understood. Research focuses on the time and temperature dependence of the Na2SO4 salt assisted, hot corrosion of SiC CMCs that are coated with a thin film of Boron Nitride (BN). Various corrosion products, reaction mechanisms and kinetics, along with the degradation and oxidation of the BN coated SiC CMC itself are studied to better understand how these materials will behave inside of marine-based turbine engines.
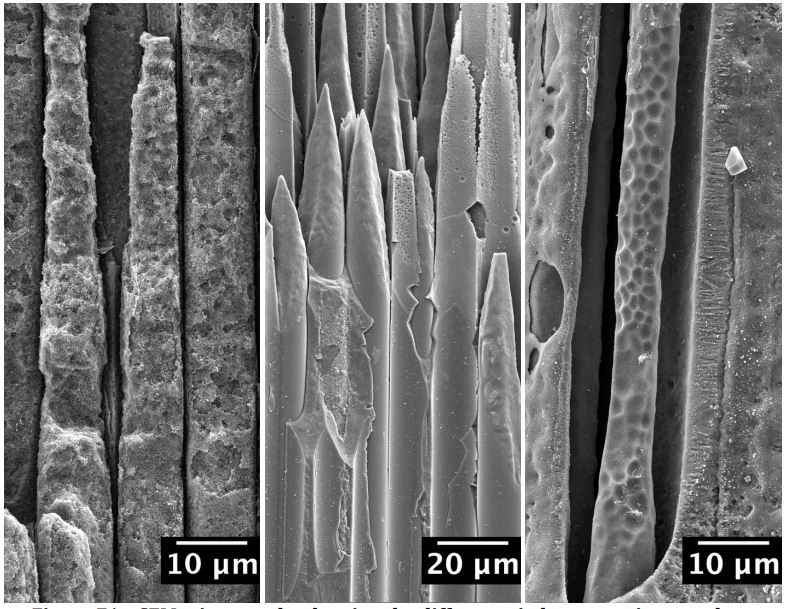
Hot Corrosion of three different SiC fiber types: Sylramic, Hi-Nicalon, and Hi-Nicalon S
Hot Corrosion of Metals
Gas turbines are used in shipboard applications with the need for high reliability and long service lives. However, in marine environments hot section turbine components can degrade due to accelerated hot corrosion resulting from the deposition of low-melting temperature salts such as Na2SO4 and MgSO4 derived from the fuel and the external environment. These salts then react with and disrupt the protective oxide layer on the surface of superalloys and metallic coatings. The Low Velocity Burner Rig (LVBR) is used to evaluate the response of superalloys and high-temperature coatings to Type II hot corrosion conditions. Up to 27 samples are simultaneously exposed to gas turbine conditions for 1,000 hours. Marine diesel doped with sulfur is combusted while an artificial seawater contaminant is added to the combustion gases. An automated system removes samples once out of every 24 hours to replicate engine cycling. Scanning electron microscopy (SEM), Energy-Dispersive X-ray Spectroscopy (EDS), and Inductively-Coupled Plasma Optical Emission Spectroscopy (ICP-OES) are used to quantify the extent of corrosion/metal loss for each material. The results will be used to select new gas turbine materials for future naval capabilities.
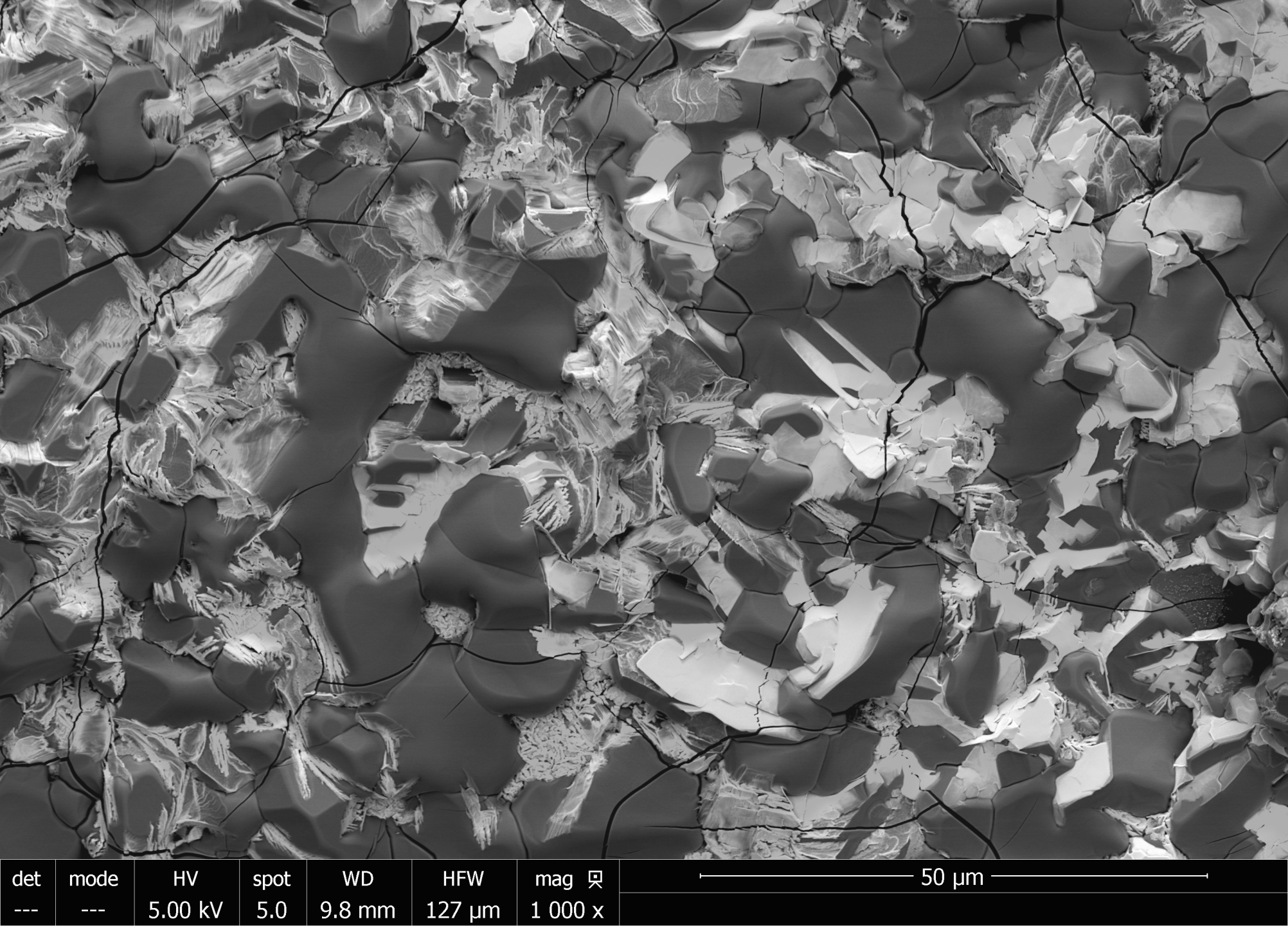
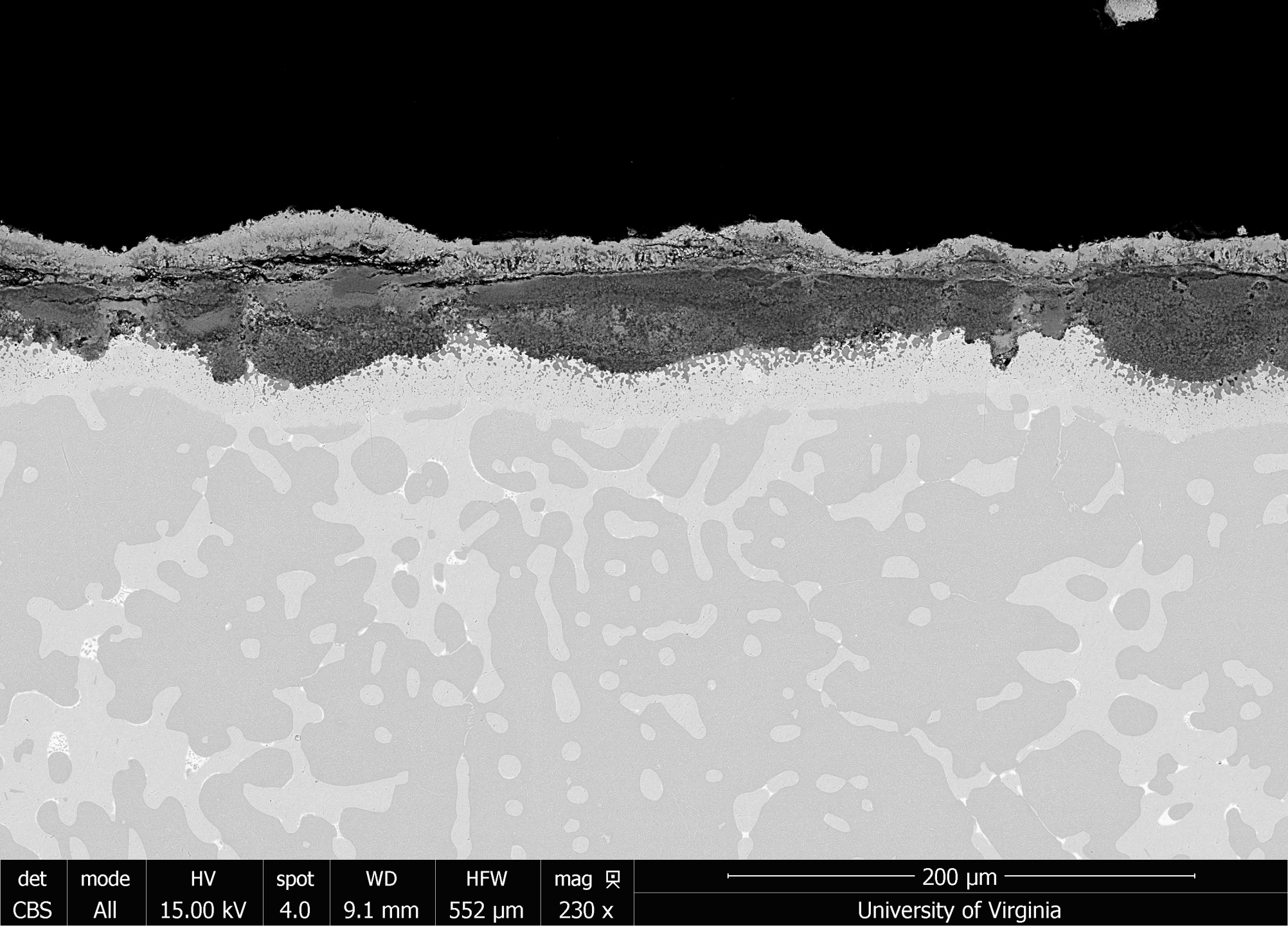
Sulfate salt deposits on a NiCoCrAlY causing Type II Corrosion
-
Time: 1:00 PM - 5:00 PMLocation: Rice 130 and Davis Commons
-
Time: 3:00 PM - 4:30 PMLocation: Rice 130 and Davis Commons
-